Opublikowano 9 September 2016
Packing of the castings takes place as per customer’s specific requirements. According to the specification, castings can be packed:
- on industrial pallets
- on EUR pallets
- on EUR pallets with level raiser
- in baskets
In order to protect and optimize delivery, castings can be:
- wrapped in film
- banded (taped) with C65 tape
- stacked
Opublikowano 9 September 2016
According to customer’s request we provide the following castings:
- Raw
- Primed with an anti-corrosive underlay
- With painted surface according to customer’s request
Opublikowano 9 September 2016
Before castings can be primed and packed there is a possibility, on customer’s demand, to treat the castings by the process of stress relief annealing. The thermal treatment is undertaken according to the internal instructions of the thermal treatment and records of the entire process are prepared in electronic and paper form.
The entire process of the thermal treatment is controlled with furnace thermocouples used for periodic checks of temperature inside a furnace. The process of stress relief annealing takes place in the gas furnace with chamber’s dimensions of 6000x3000x1700 and loading capacity of 40 tons.
Opublikowano 9 September 2016
After casting and later during cooling, the moulds are knocked out at the shock grid.
Raw castings together with pouring sections undergo shot-blasting in the shot-blaster racking machine or at the manual pneumatic shot-blasting stations.
At the final stage of the manual cleaning castings are grinded in order to obtain the final appearance.
Opublikowano 9 September 2016
Metal melting takes place in the INDUCTOTHERM induction furnace of medium frequency with the crucibles capacity of 1.5t and 3t, which has capability of simultaneous melting cast iron in one of the crucibles while upholding temperature of previously melted cast iron in the other. The current maximum capacity of the melting shop is 5000 tons/year and its extension is planned in the near future.
The melting shop uses a number of instruments to control quality of the melted metal, such as: spectrometer, tools for thermal analysis and immersion thermocouples for temperature control. Filling of the forms is undertaken by pouring ladles with a different capacity (from 0.6t to 5t).
MODIFICATION – depending on a technology and size of metal portion, is carried out at the bottom of the ladle or on the metal mirror during pouring. Spheroidization is carried out by the key metal method at the pouring ladle’s bottom.
Production of ductile cast iron is constantly increasing in comparison to grey cast iron and low-alloy cast iron and currently is around 35% of the foundry’s general production.
Opublikowano 9 September 2016
The Tarnów Foundry specializes in manufacturing single casts and small to average series (preferred batches 100-200 pieces/month). Manual forming takes place in round or rectangular flasks with maximal size of ∅ 2200 for the round flasks and 3600×1900 or 6700×900 for the rectangular flasks. The maximum weight of a casting is 4 tons.
The forms, as well as most of the cores, are made with use of continuous whirl mixers from furan mass based on reclaimed quartz sand. The Form Making Department has two Wohr whirl mixers with efficiency of 15t/h and 12t/h. The entire mould mass (including the core) undergoes process of mechanical recycling. The fully automated station of mass processing allows us to recover about 85-90% of the quartz sand.
Opublikowano 9 September 2016
The cores are made from furan mass based on reclaimed quartz sand with use of continuous whirl mixers. The used technology allows to make cores for cast manufacturing that fulfils high customer expectations both in regards to measurements and quality of the surface.
The core production department has two whirl mixers: the main one, Wohr with efficiency of 12 t/h and the assistance one AMD-4s with efficiency of 4 t/h.
Currently we are in the process of implementing shooter for cores in Cold-Box technology. The planned start date is July 2017.
Opublikowano 9 September 2016
The Pattern and Carpentry Department is making casting equipment (patterns and core boxes) necessary to manufacture casting moulds, both from wood (multiple use) and styrofoam (disposable). Apart from pattern preparation for our own production, our staff design, manufacture and repair patterns for external companies.
In 2012 we purchased the three-axle CNC milling machine together with software, what allowed to extend our production capabilities. Currently we are making casting equipment based not only on traditional 2D documentation but also based on 3D documentation.
We are making casting equipment from:
- Wood
- Epoxy resin
- Combination of materials (wood, epoxy resign with metal elements)
- Styrofoam
Opublikowano 9 September 2016
The Construction and Technology office employs qualified and experienced engineers and deals with preparation and monitoring of the production process parameters.
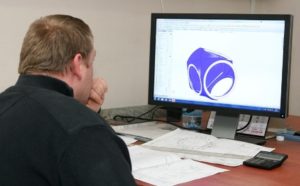
Our technicians oversee the correct course of all production processes by:
- Verification of feasibility of making a casting,
- Calculation of production costs,
- Development of relevant technology,
- Propose potential improvements in regards to technological solutions,
- Construction, design in SOLID WORKS and SOLID EDGE,
- Implementation of technology for manufacturing.
Opublikowano 9 September 2016
We manufacture castings from the following types of cast iron:
Grey cast iron
|
Type of cast iron according to EN 1561
|
Type of cast iron according to DIN
|
Type of cast iron according to BS
|
Type of cast iron according to NFA
|
Minimum tensile strength
Rm (MPA)
|
EN-GJL-200
|
GG-20
|
200
|
FGL 200
|
200
|
EN-GJL-250
|
GG-25
|
250
|
FGL 250
|
250
|
EN-GJL-300
|
GG-30
|
300
|
FGL 300
|
300
|
EN-GJL-350
|
GG-35
|
350
|
FGL 350
|
350
|
Ductile cast iron
|
Type of cast iron according to EN 1563
|
Type of cast iron according to DIN
|
Type of cast iron according to BS
|
Rm min
MPa
|
Rp0,2 min
MPa
|
A5
%
|
EN-GJS-400-15
|
GGG-40
|
420/112
|
400
|
250
|
15
|
EN-GJS-400-18
|
|
400/18
|
400
|
250
|
18
|
EN-GJS-450-10
|
GGG-45
|
450/10
|
450
|
310
|
10
|
EN-GJS-500-7
|
GGG-50
|
500/7
|
500
|
320
|
7
|
EN-GJS-600-3
|
GGG-60
|
600/3
|
600
|
370
|
3
|
EN-GJS-700-2
|
GGG-70
|
700/2
|
700
|
420
|
2
|
and other types of low-alloy cast iron containing:
phosphorus P up to 0,5%
vanadium V up to 0,28%
molybdenum Mo up to 0,5%
boron B up to 0,040%
nickel Ni up to 1,8%